Educating staff on workplace safety and protective garment care
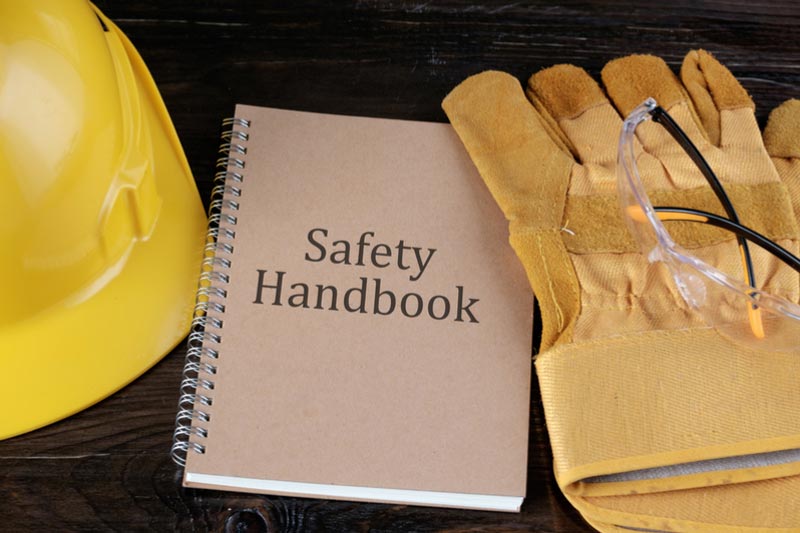
Although employers are legally required to ensure the health, safety and well-being of their workforce, every individual employee within a company still has a responsibility to protect themselves from harm, and they should take the appropriate measures to do so. This means that as a basic requirement, all workers need to follow any safety advice and instructions issued by their employer.
In terms of health and safety, the information an employer advises their workers on will be in regards to completing their tasks and responsibilities as instructed, using any equipment they’re provided with correctly, wearing appropriate protective garments for their working environment, and maintaining a good level of personal hygiene when working with particular materials and substances. As an example, NIOSH (The National Institute for Occupational Safety and Health) advises that anyone who is exposed to silica dust washes their hands before eating, drinking, or smoking, and showers and changes out of their workwear before leaving the site they’re working on.
This is because silica dust is extremely fine and difficult to detect, and it can cause a number of harmful lung diseases, such as silicosis, chronic obstructive pulmonary disease (COPD), and even lung cancer if it’s breathed deep into your lungs.
However, silica dust isn’t the only hazard industrial employees may face when working, and there are various reasons you should be educating your staff on workplace health and safety. As well as keeping your employees safe (which ensures your compliance with regulations) it will also help your workforce to develop a positive attitude towards health and safety, and enable you to better manage health and safety in the workplace.
It’s very easy to think that an accident won’t occur in your workplace, but statistics show that last year, 70,116 non-fatal injuries and 137 fatal injuries to workers were reported. Additionally, there were 1.3 million cases of work-related ill health (new and withstanding) in 2016 and 2017, and during that same period, 25.7 million working days were lost to work-related ill health.
So, how do you take the appropriate steps to educate your employees on health and safety (including caring for any protective workwear they’re provided with, and are required to wear on-site)?
Carrying out risk assessments is a legal requirement for any business owner, so this should be the first step you take. As HSE (the Health and safety Executive) explains, a risk assessment will require you to identify appropriate preventative measures for every hazard in the workplace, whether it’s something as large as working with chemicals and electricity, or something as minor as draws being left open, or wires covering certain areas of the floor.
When carrying out your risk assessments, remember that a hazard is anything that can cause harm to you, your employees, or any visitors to your premises, and the risk is the chance that this hazard could harm someone. You’ll need to determine if the risk is high or low, and how serious the harm it has the potential to cause could be.
If your company has less than five employees, then you won’t need to write anything down. However, to educate your staff on ensuring health and safety in the workplace, you’ll need to consult with them on any risks you’ve identified. This will include providing them with information on how your business is protecting them, additional steps they can and should take to prevent accidents from occurring, and what they should do if an incident does occur when working.
One way you can prevent workplace-related ill health and accidents is by providing your workers with suitable protective workwear (such as high visibility and flame resistant garments). However, it’s vital for you and your employees to keep them properly maintained to ensure their effectiveness, and their compliance with the relevant legislation.
The easiest way to ensure your workwear is properly cared for is by laundering it through an industrial laundry service, such as the one provided by
phs Besafe. We prevent wear and tear by laundering the garments at 40 degrees, and using a gentle specialised detergent. They’re also gently dried in a convected tumble dryer to prevent damage being caused to zips and other features.
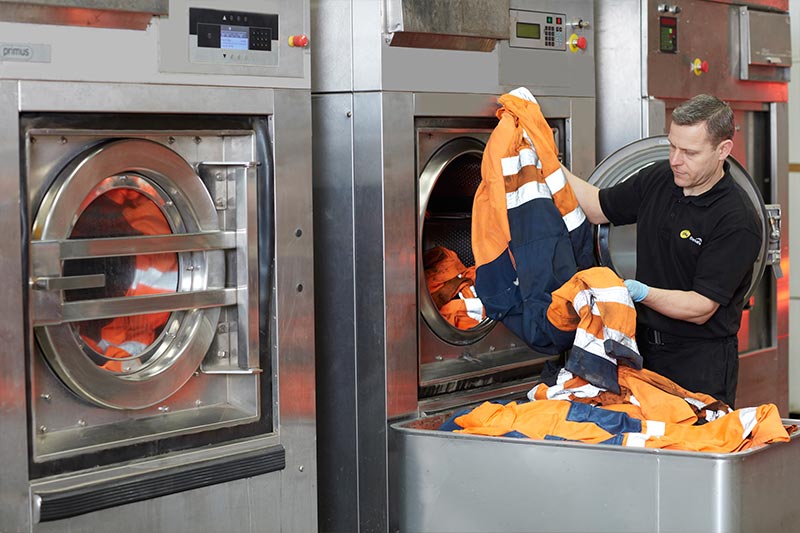
As part of our industrial laundry service, we also inspect the workwear for repairs and alterations, and carry these out (if needed). Nonetheless, you should still instruct your employees to check their safety workwear for damage after every wear. This includes tears, cuts, holes, punctures, and fraying, as well as discolouration, or the workwear softening or hardening, as these can be signs that the workwear is contaminated after coming into contact with potentially harmful chemicals.
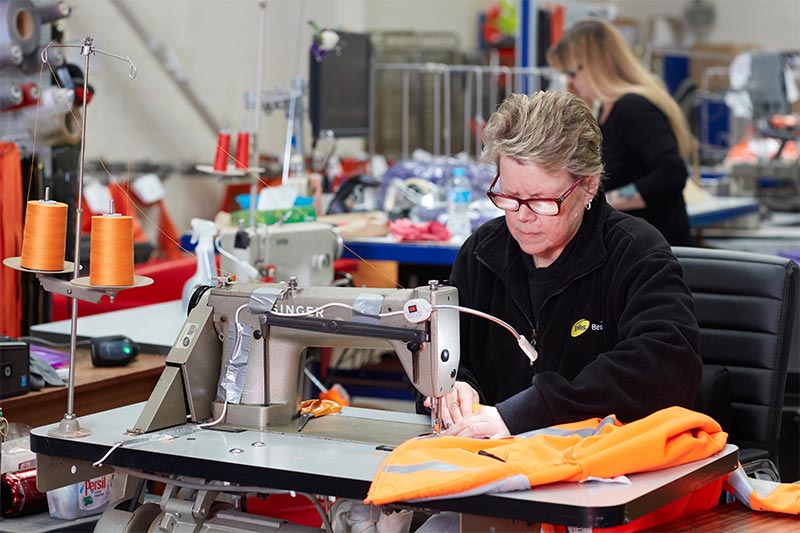
To prevent the risk of contamination, you should also advise your workers to only wear PPE (Personal Protective Equipment) and protective workwear when working on-site, and to securely store this in a locker at the end of each working day.
To find out more about our high visibility and flame resistant protective workwear ranges, industrial workwear laundry service, and secure workwear destruction service, contact phs Besafe.