The importance of wearing and maintaining protective workwear in the colder months
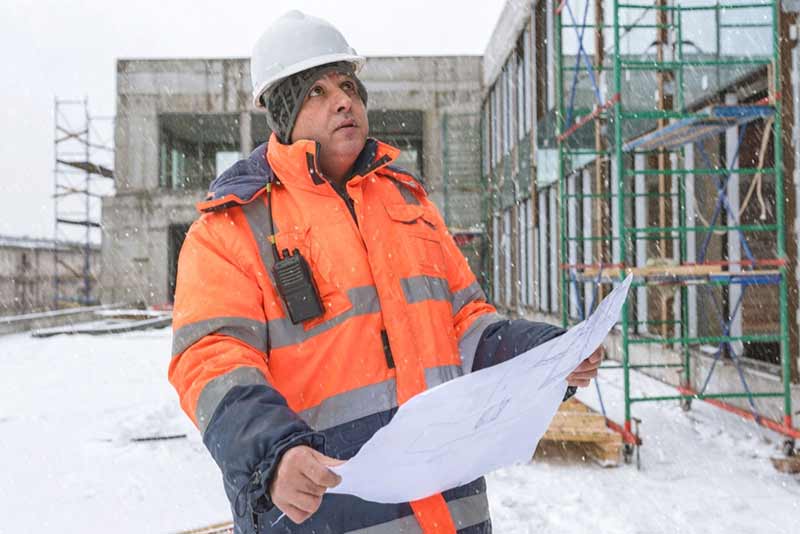
Providing your workers with suitable protective workwear is an essential part of ensuring their health, safety and general well-being. At the minimum, it should be comfortable, durable, compliant with the required safety standards (such as EN471 for high visibility clothing), and it should also be suitable for the employee’s specific working environment. Another factor that shouldn’t be overlooked is the fact that the protective workwear you provide should also be appropriate for changing weather conditions, whether it’s warm and sunny or cold and rainy. This is especially important as we head closer to winter, and you should be educating your workforce on the importance of wearing and maintaining protective workwear in the colder months.
Safety workwear is worn by employees in a host of environments that leave them exposed to nature’s elements. These include construction sites, railways, aggregates, ports, and quarries (to name but a few). This leaves at risk of encountering an array of potential hazards in the colder months, from hypothermia to slips, trips and falls.
As an employer, your legal and moral obligations go beyond supplying your workers with appropriate protective workwear and PPE (Personal Protective Equipment); it should also be correctly laundered, stored and maintained too. Here is the vital legislation and statistics you need to be aware of, as well as what you should do to ensure the safety of your workers in winter conditions…
The legislation you need to know
As an employer, you have a legal obligation to ensure the health and well-being of your workers, with The Health and Safety at Work etc Act 1974 (HASAWA) being “the primary piece of legislation covering occupational health and safety in Great Britain”. It outlines that all employers should ensure (so far as is reasonably practicable) the health, safety, and welfare of their staff at work. This in terms of systems of work, the handling, storage and transportation of articles and substances, and the condition of the place (or places) of work. The Act also dictates that as a general duty of employers to their employees’, they should provide the necessary ‘information, instruction, training and supervision’ to ensure health and safety in the workplace.
For sectors such as construction, industrial, manufacturing, aggregates and the emergency services, your duty as an employer also includes supplying workers with suitable protective workwear. According to Regulation 4 of the Personal Protective Equipment at Work Regulations 1992, suitable PPE (Personal Protective Equipment) must be provided to employers who are exposed to risks to their health and safety while at work. However, this should be “except where and to the extent that such risk has been adequately controlled by other means which are equally or more effective.”
PPE for workers includes (but is not limited to) helmets, goggles, gloves, boots, ear plugs, high visibility garments, flame resistant garments, and different types of respiratory protection, such as dust masks, gas masks and particulate filters.
As part of your obligation to supply protective workwear you should also ensure that the correct type is worn for the environment and task at hand. As an example, high visibility workwear is vital for areas with low light levels particularly where dangerous heavy machinery is being operated. Flame resistant workwear needs to be worn when employees are involved in welding, cutting or grinding, if they’re at risk of coming into contact with flame, or they’re handling corrosive chemicals.
Facts and figures around winter health and safety
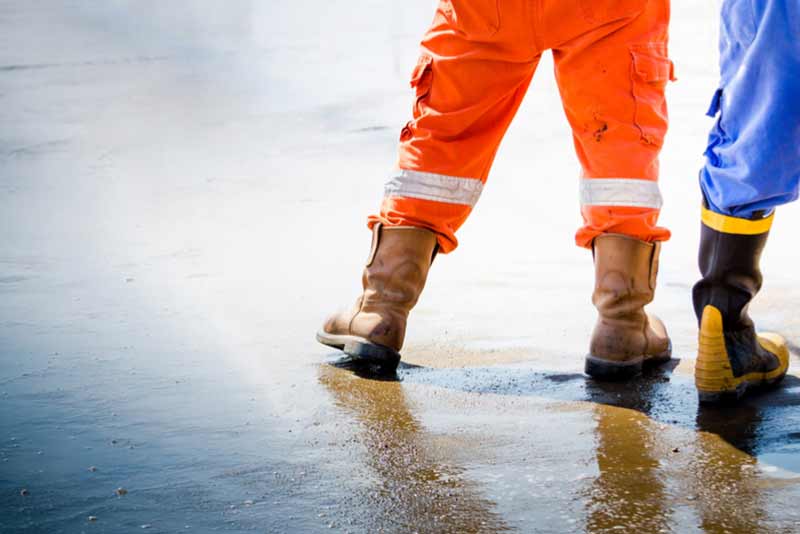
Protecting your employees is a legal requirement all-year-round but it’s especially vital in the autumn and winter months. This is due to increased hazards and health risks, which are caused by their harsher weather conditions. According to statistics from the Health and Safety Executive (HSE), slips, trips and falls (on the same level) were the highest cause of workplace injury in 2016/17. Many factors, such as early mornings and evenings getting darker and the increased risk of rain, snow and ice on the ground, make these types of incidents more likely to occur in the colder months.
HSE statistics also shows that being struck by a moving or falling object is the third largest category of workplace incidents that are reported each year. In fact, they’re said to cause around 700 injuries a year of which 100 are fatal incidents. Again, lower light levels in autumn and winter can increase the risk of this type of incident occurring in the workplace, particularly if working in industrial areas.
Falling and moving objects that can cause serious injury in the workplace include handheld tools (such as hand knifes), self-standing objects (such as gas cylinders), barrels and kegs, and pedestrian operated vehicles, pallet trolleys and racks.
Hypothermia, which causes your body temperature to drop dangerously and can be fatal, can be caused by wearing inadequate clothing in cold weather conditions, falling into cold water, and getting cold when wearing wet clothes. These become considerable risks when working outdoors, particularly in autumn and winter. Statistics show that in England, 25,000 extra deaths are caused by hypothermia each year which is a worrying statistic. Fortunately, it can be prevented by employers and their employees taking appropriate precautions before working in adverse weather conditions.
Our top tips for protecting employees in winter
Ensure they can be seen in low light levels
With daylight hours reducing as we head closer to the colder months, many construction and industrial employees are going to be carrying out their everyday tasks in lower light levels where they might not be seen or be able to see. This greatly increases the likelihood of accidents such as being hit by moving vehicles or heavy falling objects. To keep them visible, supply them with the right type of high visibility workwear for their working environment. As an example, our Glow Gear workwear reacts to changing levels of light, making it particularly great for winter.
As an employer, it’s also your duty to ensure that the high visibility workwear you provide is compliant with the relevant safety standards. This includes the EN 20471 (European Standard) which is split into 3 classes to assess a garment’s suitability and durability. At phs Besafe, our workwear conforms to the EN 20471, as well as the Railway Group Standard (GO/RT 3279).
Protect employees from the elements
To reduce the risk of your employees developing colds, flu and hypothermia as a result of their working environment, you should be doing all you can to keep them warm and dry when working outdoors. In the case of jobs that require protective workwear, this means providing them with a range of different garments that can be layered to suit changing weather conditions, such as short sleeve and long sleeve polo shirts, jackets, and coveralls.
When choosing high visibility workwear for employees working in colder weather, you should also be ensuring that it has been designed to protect them from the elements. Features to look out for include waterproof panels and knee pad pockets, as well as zip chin guards and heavy duty zips to reduce the wind chill effect. For extra warmth and comfort, the Soft Shell Jacket from our Glow Gear range is also fleece lined, yet lightweight.
Keep workwear clean and maintained
With the autumn and winter months bringing more wind and rain than spring and summer, your staff’s safety garments are far more likely to be soiled with mud and other dirt from the great outdoors. This doesn’t just make the garments more uncomfortable to wear; it will also reduce the wearer’s visibility. Not only that, but being soiled by heavy mud can also damage the garment’s fluorescent material and retroreflective tape. One way to combat this is by choosing workwear with a stain release finish which works to prevent contaminants from soaking into the fabric.
Having the garments laundered using an industrial laundry service for high visibility workwear will also help to ensure your employee’s workwear retains its high visibility properties for longer. At phs Besafe, our laundering process is designed to be tough on oil and grease, while being gentle enough to protect the garment’s reflective fabric, reflective tape, as well as any zips or logos.
At phs Besafe, we provide our protective workwear supply and laundering service to over 3,000 UK sites, with our clients including Arriva, Whale, and Aggregates Industries. Whether you want to rent or buy workwear for 2 or 2,000 employees, we can provide a tailored service to suit your needs. To find out how we can help your business, contact us today.